High speed and acceleration of Diakont electric actuators allow to reduce the time of welding gun opening and closing. A specially designed 10-pole synchronous motor allows performing more welding spots without overheating compared with competitors. DA99 Diakont actuator can make 30 welds/minute at high force without need for additional cooling.
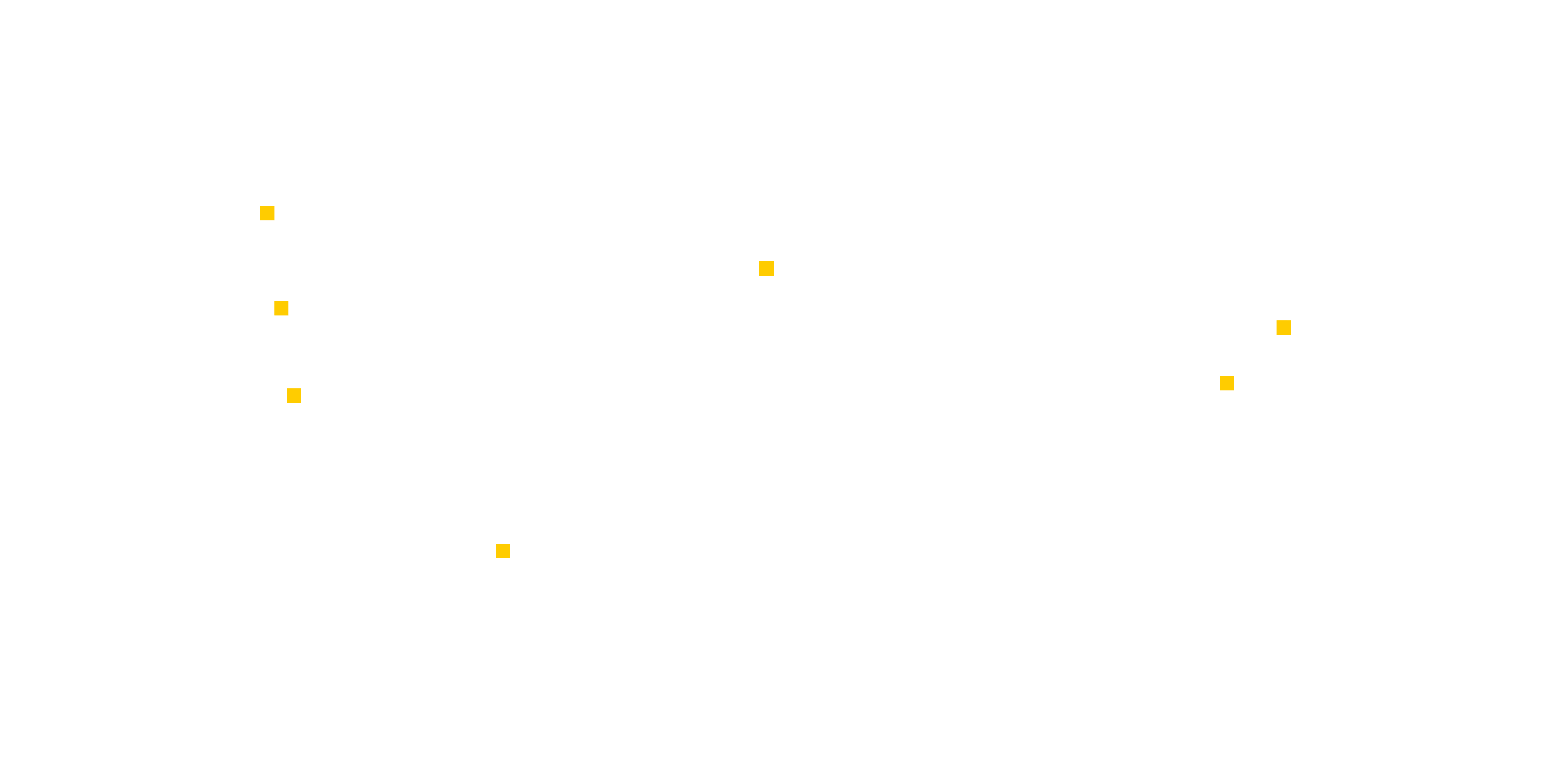
The special in-house design and manufacturing of Diakont actuators and its components, from roller-screw to the housing allows to keep the quality at high level ensuring stable operation even at stressful requirements. Protective features such as triple sealing provide additional advantages.
Integrated and robust design of Diakont roller-screws and special know-how technologies of metal hardening provide our products with exquisite lifetime characteristics capable of bearing over 30 million weld cycles.
Diakont servo actuators save time on maintenance not only because of their high quality and reliability. Such a simple procedure as grease adding can also be done very easy through a zerk on the housing and requires to be done only once in 15 million cycles.
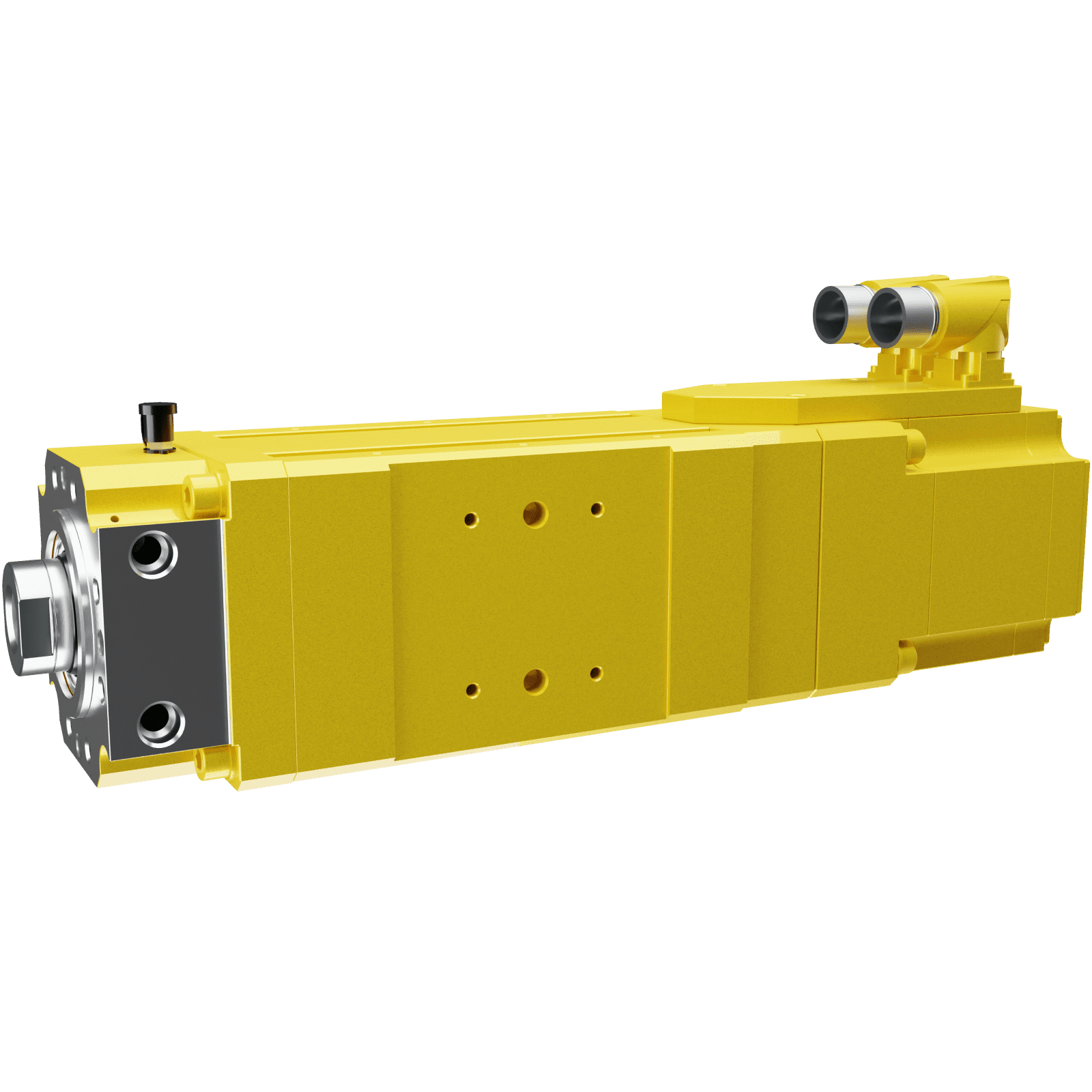
Max speed: 750 mm/s
Frame size: 99x99 mm
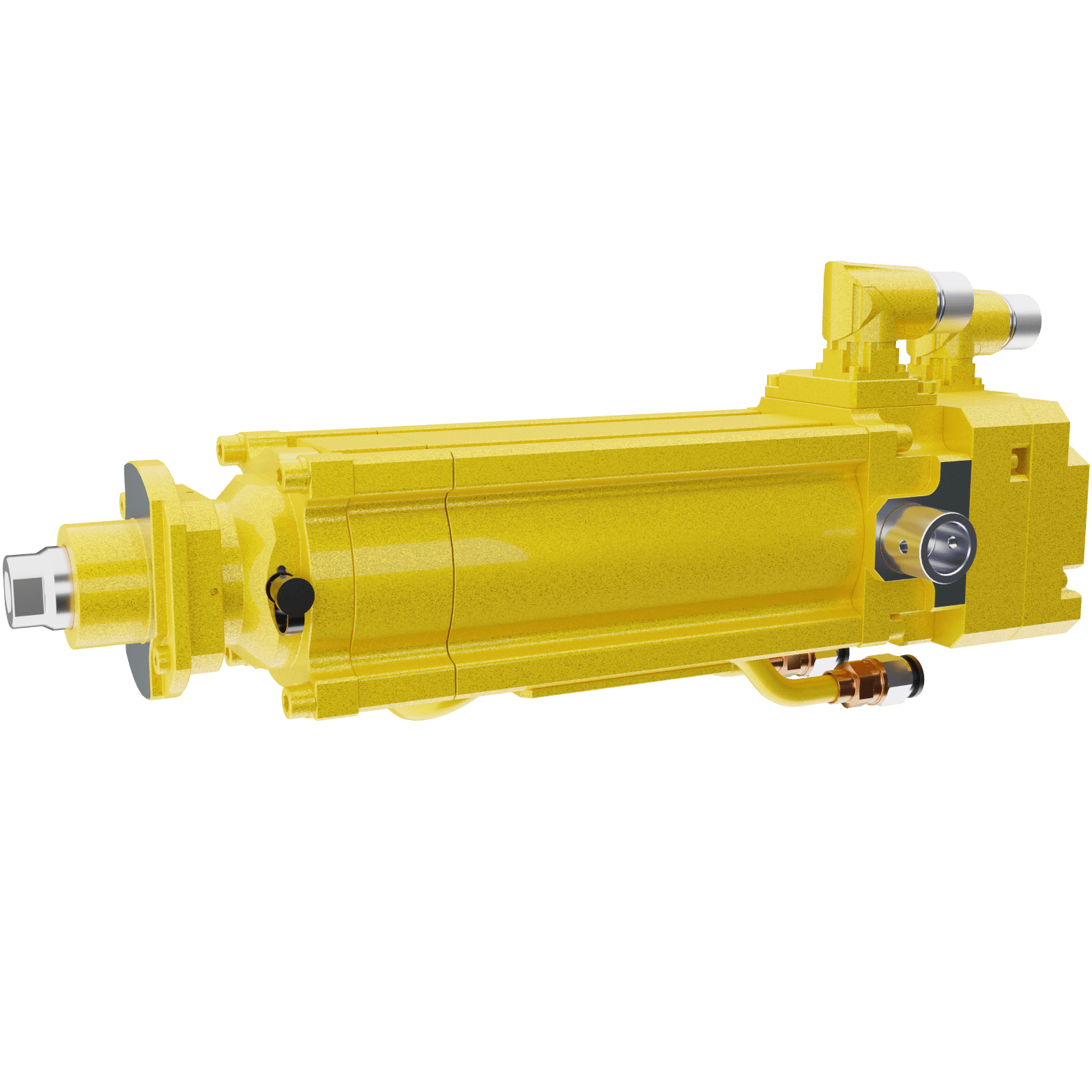
Max speed: 650 mm/s
Frame size: 78x78 mm
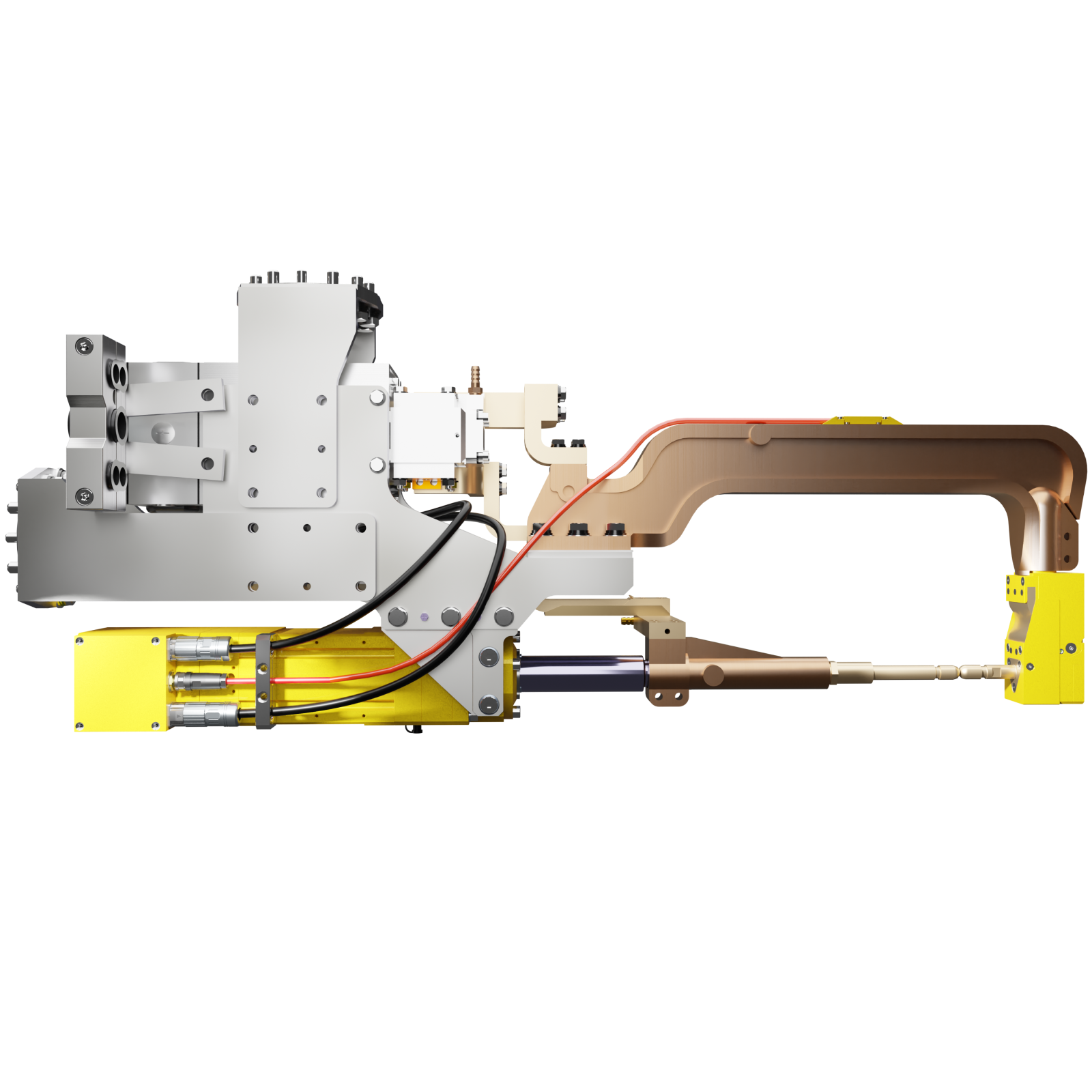
Force repeatability directly impact consistency of welding quality and is influenced by a number of factors, specific to spot-welding applications
- Variability of the actuator motor torque, arises when the electrode force requirement changes, due to cap wear and thickness of the material being welded
- Housing temperature; specially grease temperature
- Robot controller type
- Speed of electrode contact with the metal sheet. The lower the wedding force, the stronger the influence of electrode contact speed
- Presence of water cooling directly on actuator
- Degree of the welding gun deflection
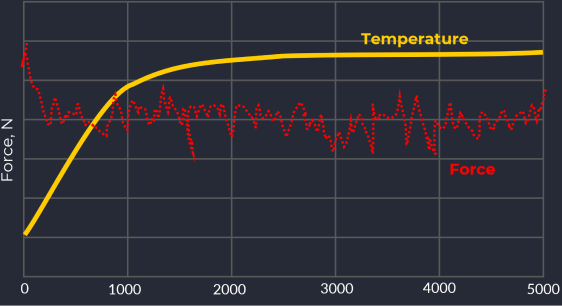
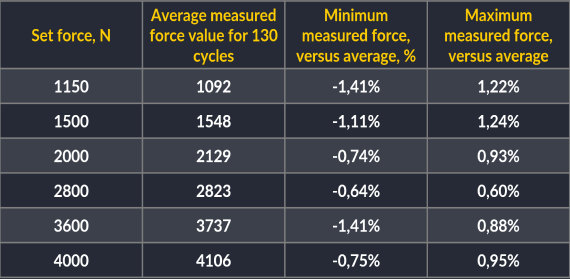
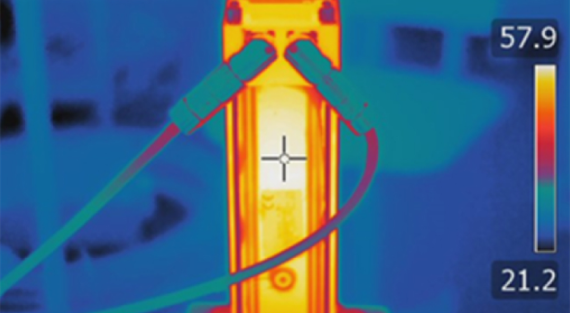
Stress tests were conducted with Diakont actuators, which showed a possibility to make up to 30 welds/min with 0.5 s welding pressure @5kN without additional cooling. It can be seen from the temperature analysis image that the hottest spot on the housing didn’t exceed 60℃ during this test.
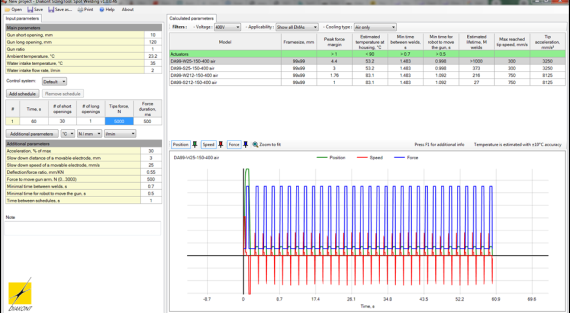
For the convenience of customers Diakont has developed a Sizing Tool – software which calculates actuators performance at designated weld cycle parameters. It is possible to see which actuator models fit the requirements of the specific welding cycle. Sizing Tool is based on Diakont in-house developed CAD software and lab verification tests
Actuator housing provides secure protection from contamination and water ingress. Smooth cylindrical rod goes through multiple sealing, while rod scraper prevents sealing from damaging by welding sludge. Thanks to these features, Diakont actuators provide reliable perform ance even when actuator is installed vertically, when water emerged during change of welding caps flows directly onto actuator. A special test bench with a constant water flow against the actuator was assembled to verify absence of any water leakages inside of the actuator.

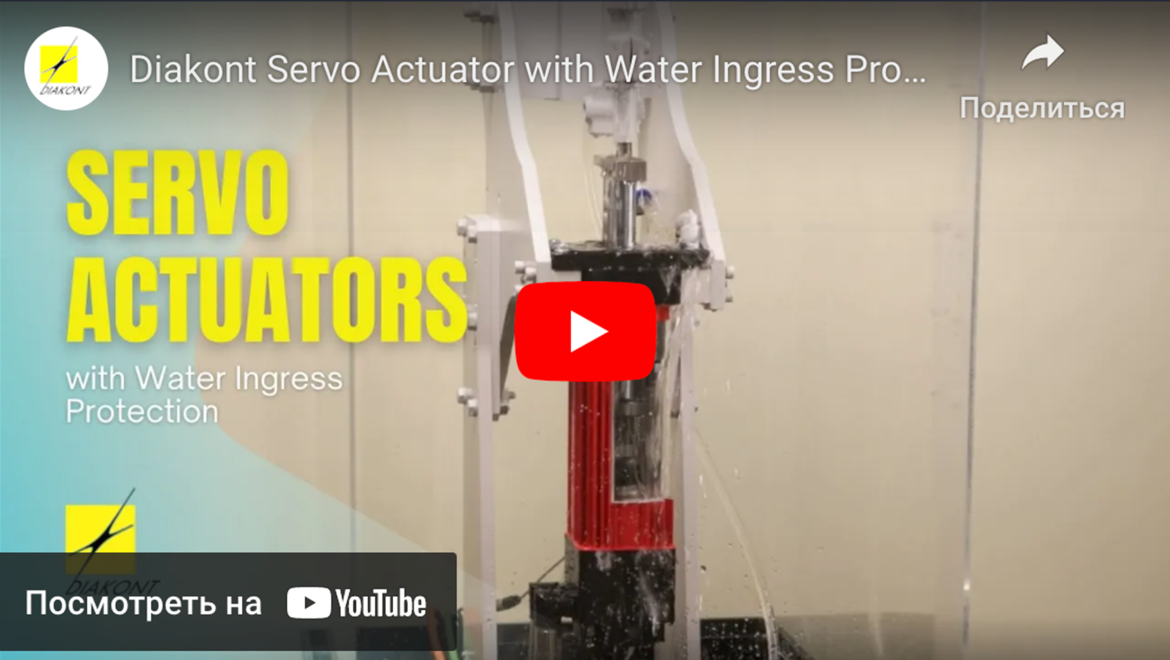
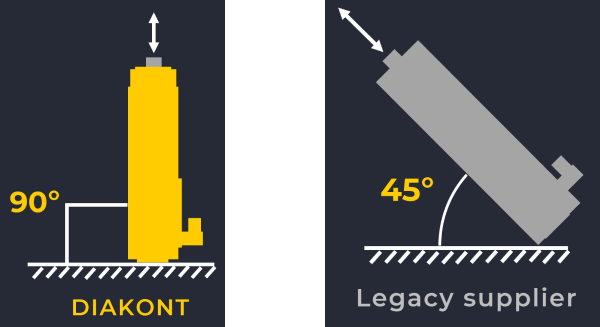
Over several years Diakont has conducted several endurance tests at specially designed test benches imitating operation at real spot welding guns with duty cycles involving maximal pressing force. The aim of the tests was to verify whether all the components are robust enough to withstand the lifetime requirements even at maximal duty cycles. During the tests no special maintenance or refurbishment was conducted.
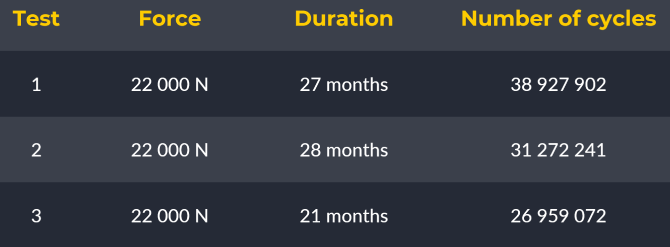
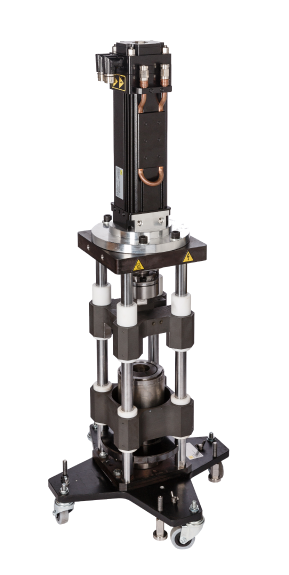
Unified design of Diakont allows compatibility with all major weld gun models without a need for specific modifications and longer lead times as a results. The housing and mounting dimensions fit to majority of X- and C- weld gun configurations.

Diakont has completed integration with all major robot manufacturing brands, which means that our actuators have verified performance and setting with control systems of these robots. For each robot actuators are equipped with corresponding position feedback sensors.
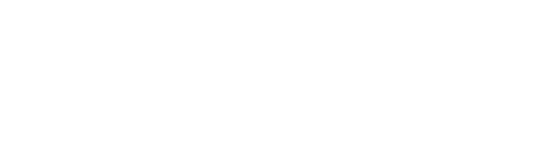
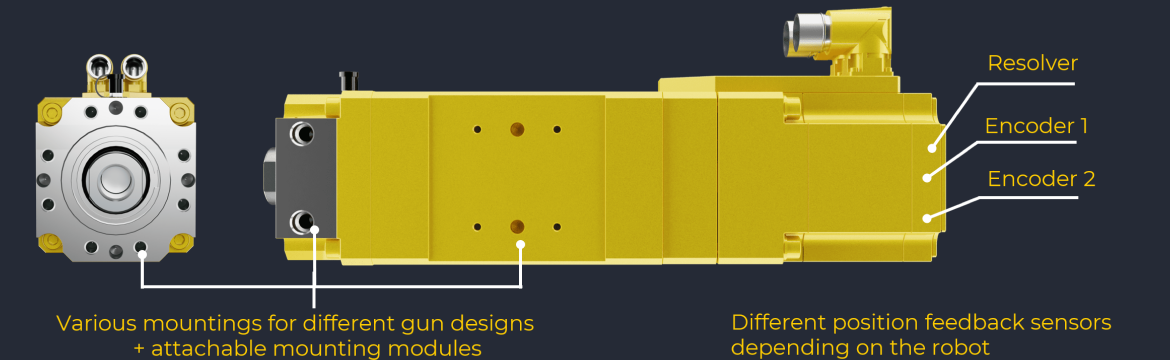