The need to move in each injection cycle in full accordance with the given motion profile places strict requirements on the positioning accuracy of the valve actuator. The required performance was achieved through direct drive technology (pin is directly placed inside the motor rotor and controls the valve without additional mechanical connections) and a high precision encoder as a position feedback sensor. Such absolute encoder allows positioning mechanisms of molding machine and molds with an accuracy of 0.01 mm and flexibly control their speed and acceleration.
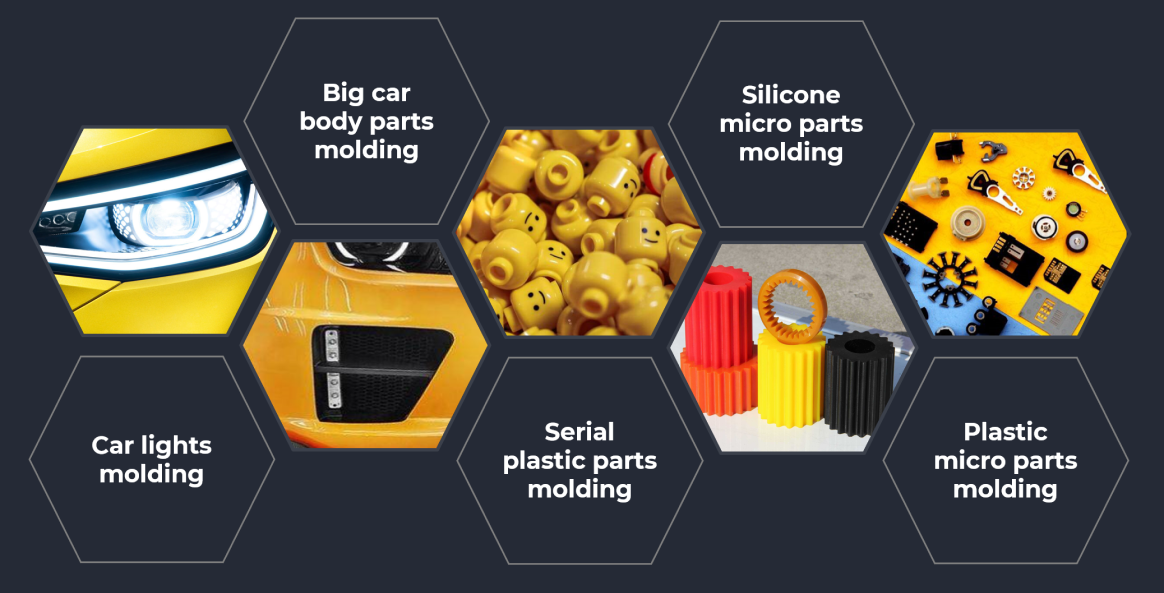
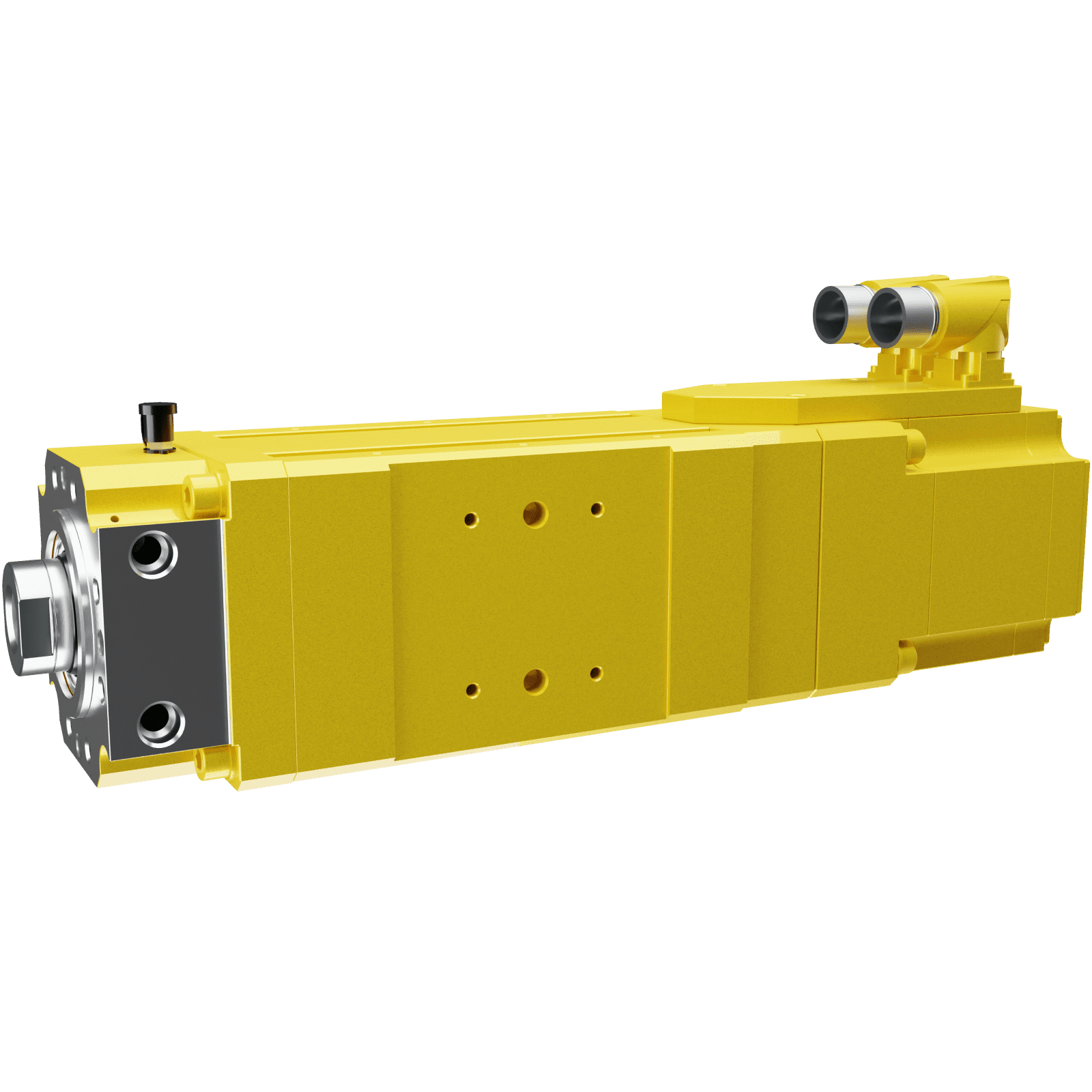
Max speed: 750 mm/s
Frame size: 99x99 mm
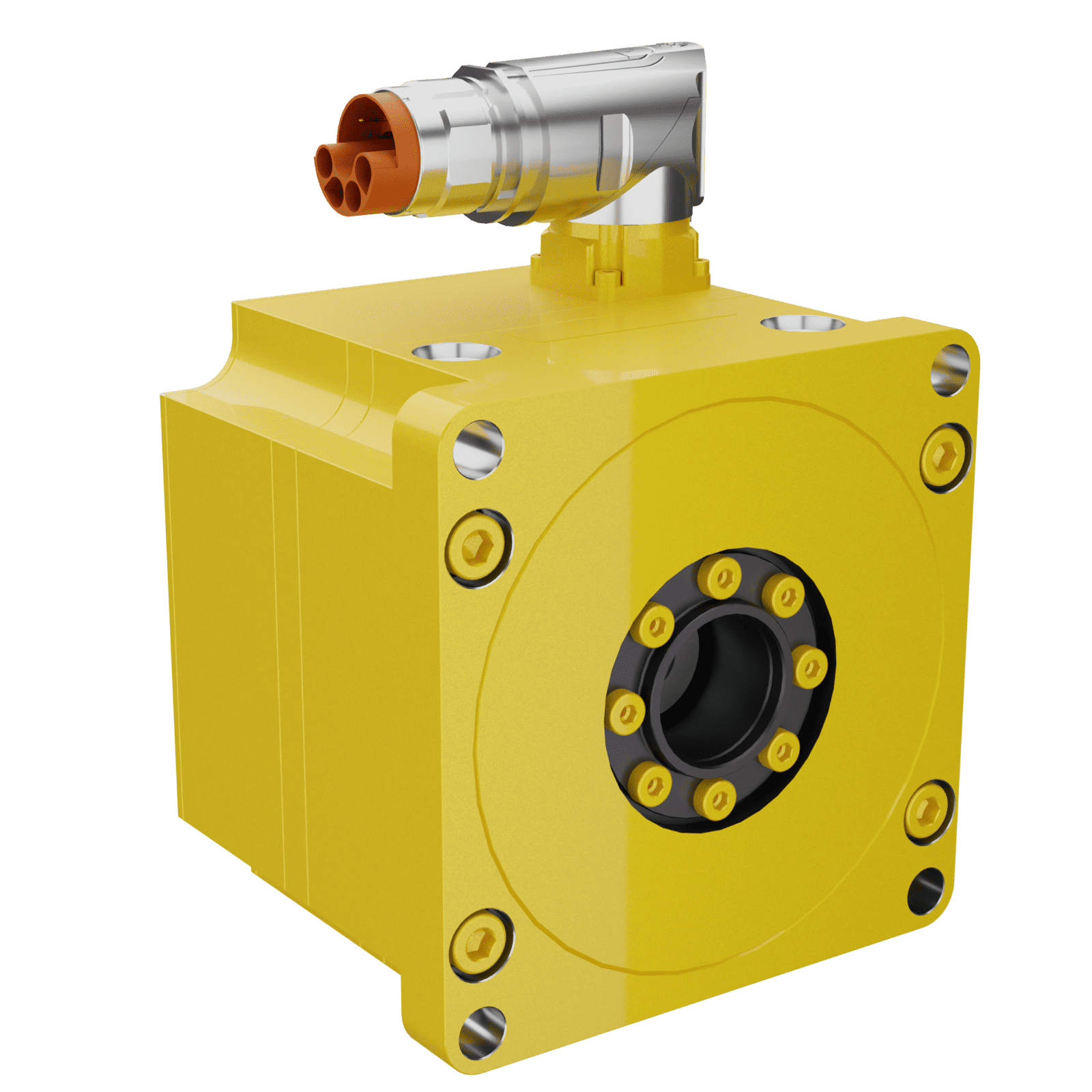
Max speed: 80 mm/s
Frame size: 108x108 mm
Injection molding through hot runner systems is indispensable in the automotive industry for the production of headlights, front panels and other complex parts where high-precision control of plastic flow is required.
The use of servo-electric valves in casting provides a number of undeniable technological advantages for manufacturers, such as the elimination of hesitation lines, the transfer of joint lines to a non-critical zone and increased process stability. However for a long time a weak spot in using electromechanical solutions for valve control was a large size compared to hydraulic actuators which involved the necessity to make large cavities for them, increasing mold costs and weakening them.
Diakont has created a breakthrough compact solution that provides precise and reliable control of the movement of the locking needle in the valve gate and does not require large cavities inside the mold.
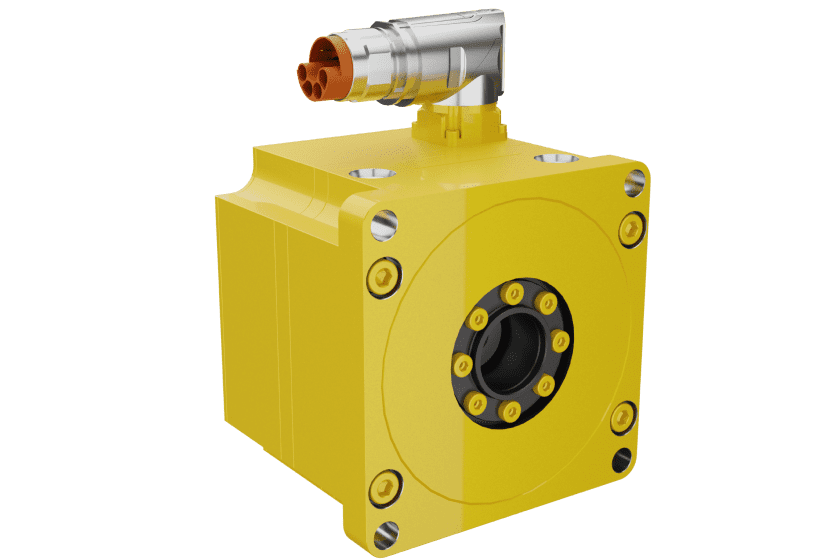
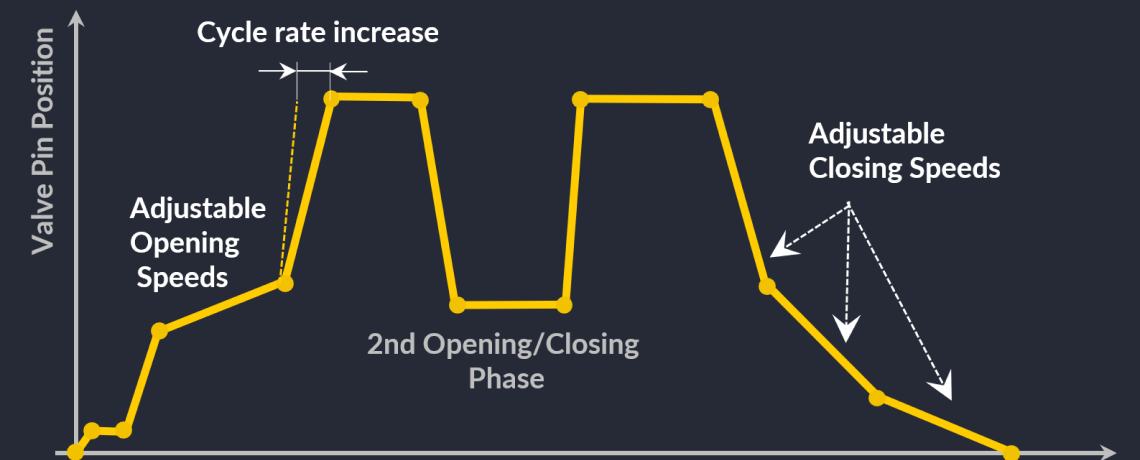
Diakont engineers were faced with the task of creating an electric valve actuator that does not require a significant increase in the cavity for its placement in the mold compared to hydraulic cylinders of the same force.
To achieve this goal, Diakont engineers have developed a unique design of a compact and lightweight direct drive, mounted on the hot runner manifold coaxially with the valve gate.
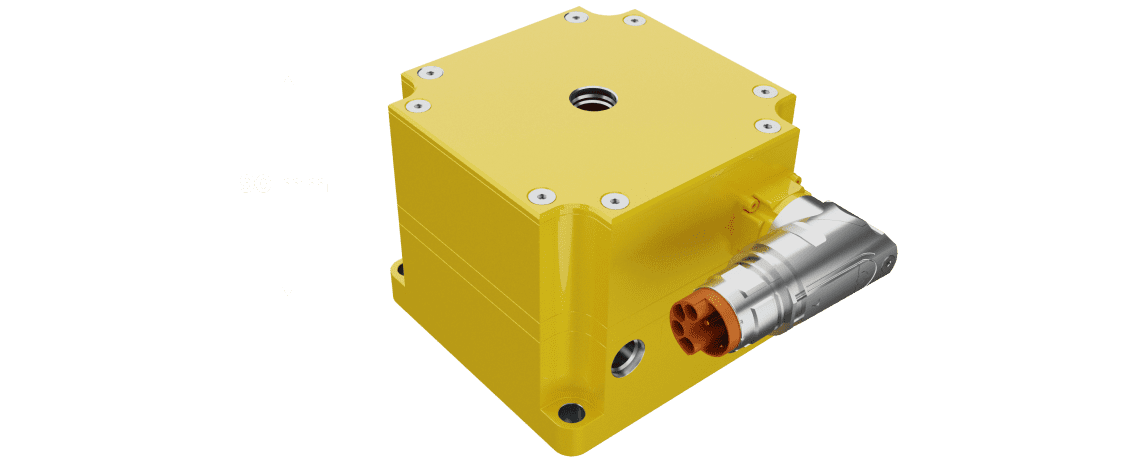
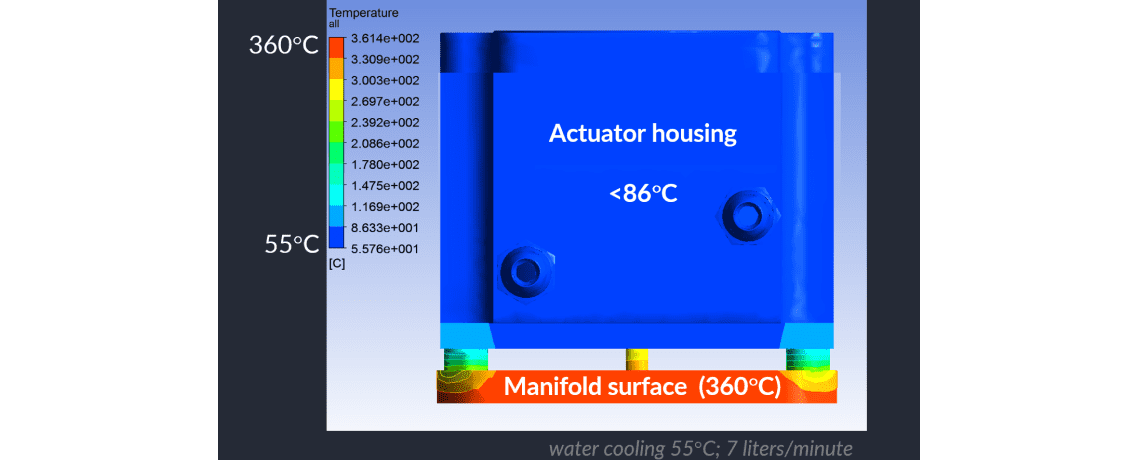
For reliable operation when mounted on a manifold, a cooling unit was built into the design of the actuator. Taking into account usually moderate quality of the shop cooling water, the possibility of easy cleaning of the built-in cooling channels was provided as well.
A special temperature resistance test was conducted in Diakont lab which showed that the actuator can operate safely under hot environmental conditions.
Electrical roller screw actuator, unlike pneumatic and hydraulic systems, does not require additional energy conversion to run the compressor and does not consume energy during pauses in operation, which reduces the cost of consumed electric energy by 3-4 times.
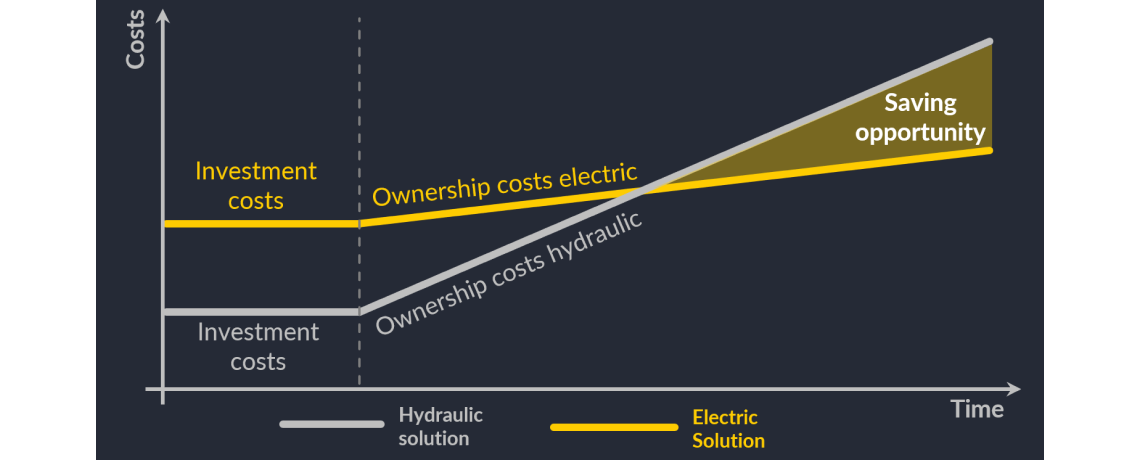
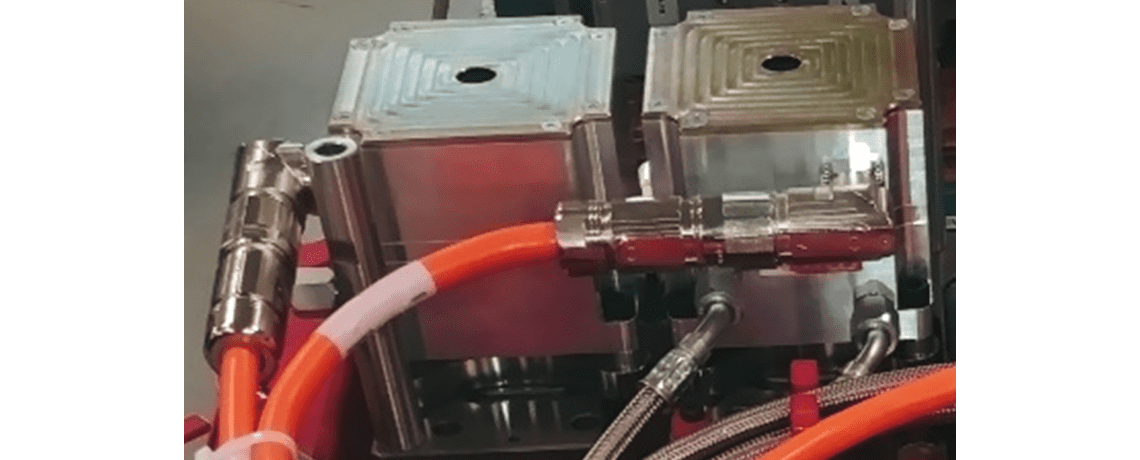
The standard solution for the actuator connection is one cable for power signals and a second cable for sensor signals. To simplify the design, Diakont engineers have implemented a single cable interference-resistant actuator connection. This simplifies the wiring and installation of cable lines and reduces labor and cost.
In order to expand technological capabilities, increase the energy efficiency of the enterprise and the stability of the process of casting polymer products, manufacturers are increasingly turning to the use of servo-electric drives in injection molding machines.
The special requirements for motion control in injection molding, as well as for surface quality and stability of geometric sections, are reflected in the line of compact electric Diakont actuators operating on an inverted roller-screw transmission and combining high force, repeatability, positioning accuracy and temperature resistance.
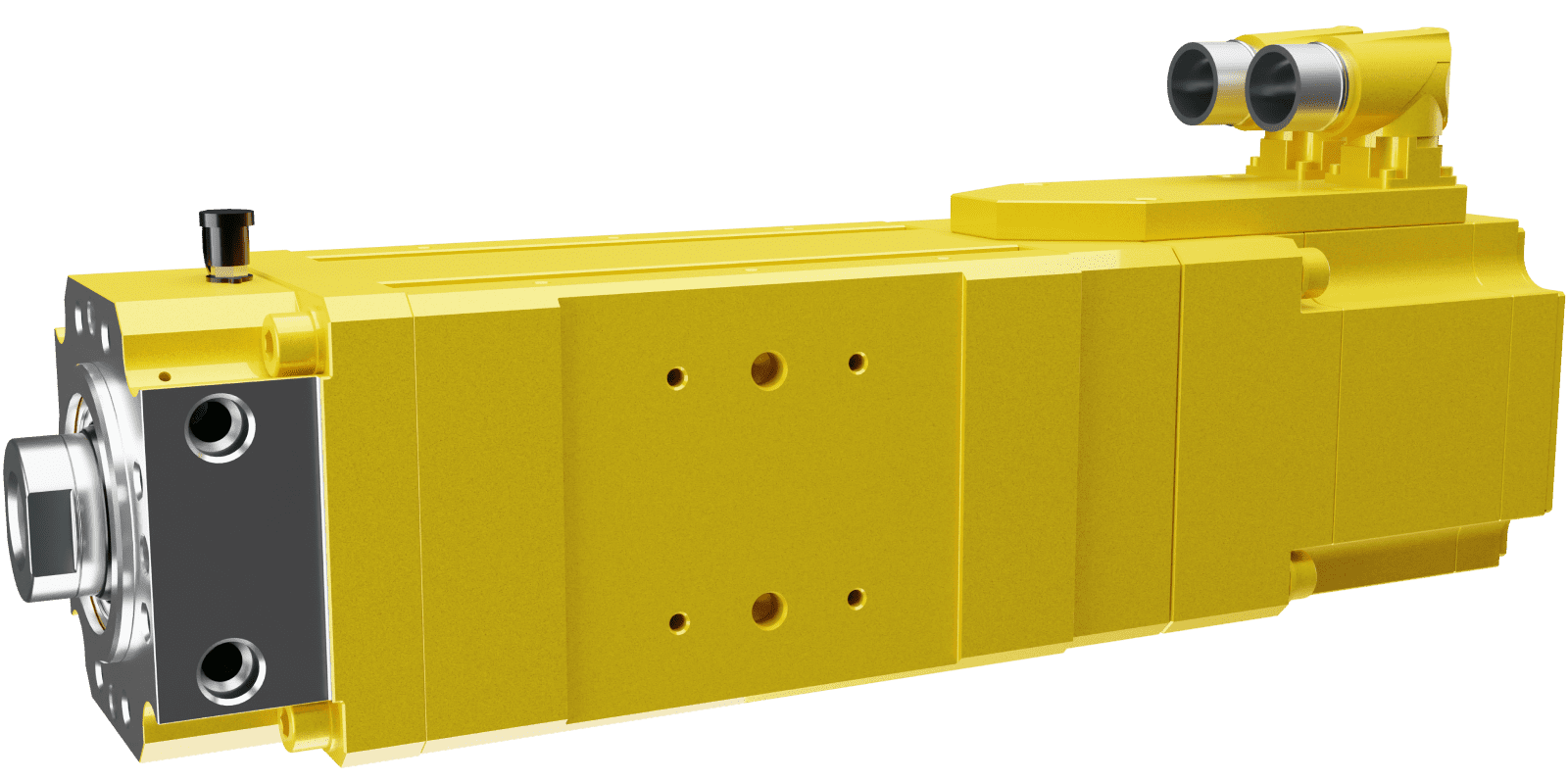
Unlike the hydraulic cylinder, the Diakont electric actuator allowed positioning the plunger with an accuracy of 0.05 mm, which significantly increased the quality of thin-walled products due to an increase in the dosing accuracy of the injected material, an increase in the uniformity of the distribution of the material, ensuring the stability of the weight of the products.
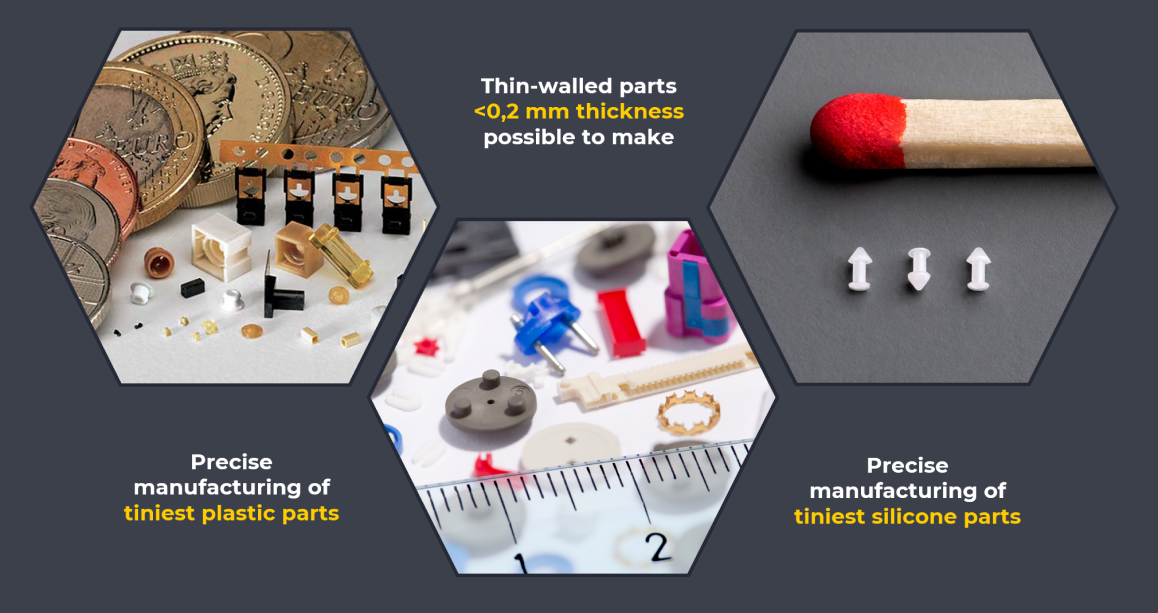
High speeds and forces
When injected, the plunger develops a force of more than 1000 kg at a speed of up to 500 mm/s. Due to the small size of the machine, the space for the plunger actuator is very limited. To minimize the dimensions, an actuator was used in which the motor is integrated with a mechanical transmission.
Simple setup
Diakont actuators can be easily customized for various conditions, cycles and work accuracy or implemented into existing production cycles without significant modification of the machine design.
Embodying the concept of integrated design, they can be equipped with built-in force and position sensors and a frequency converter integrated into the body structure, which provides multi-level control and management of each element of the machine.
Actuators «Diakont» are easy to operate - maintenance is performed much less frequently, is less laborious and requires the participation of only 1 specialist. Oil change is carried out without dismantling and disassembling the actuator.