Robotic spot welding lines for car bodies consist of individual welding cells, each of which includes a robot, welding tongs and control equipment. Traditionally used welding cells have a number of disadvantages that adversely affect the reliability of achieving welding quality and productivity. Firstly, actual welding force at electrodes differs from the set one because of the external influencing factors, such as wear of the gun or temperature change. Secondly, delivered force at each electrode might differ from each other due to variations of car body or parts position at the tooling. Productivity might be decreased because of the lower speeds limited by robot control settings. Some process functions, such as gun equalization due to gun flexion and approaching the weld spot are also not fully efficient as they are energy inefficient and require more time when performed by a robot. Finally, the processes of setting the line, retuning and maintenance procedures such as calibration are also time-consuming and require high qualification of personnel.
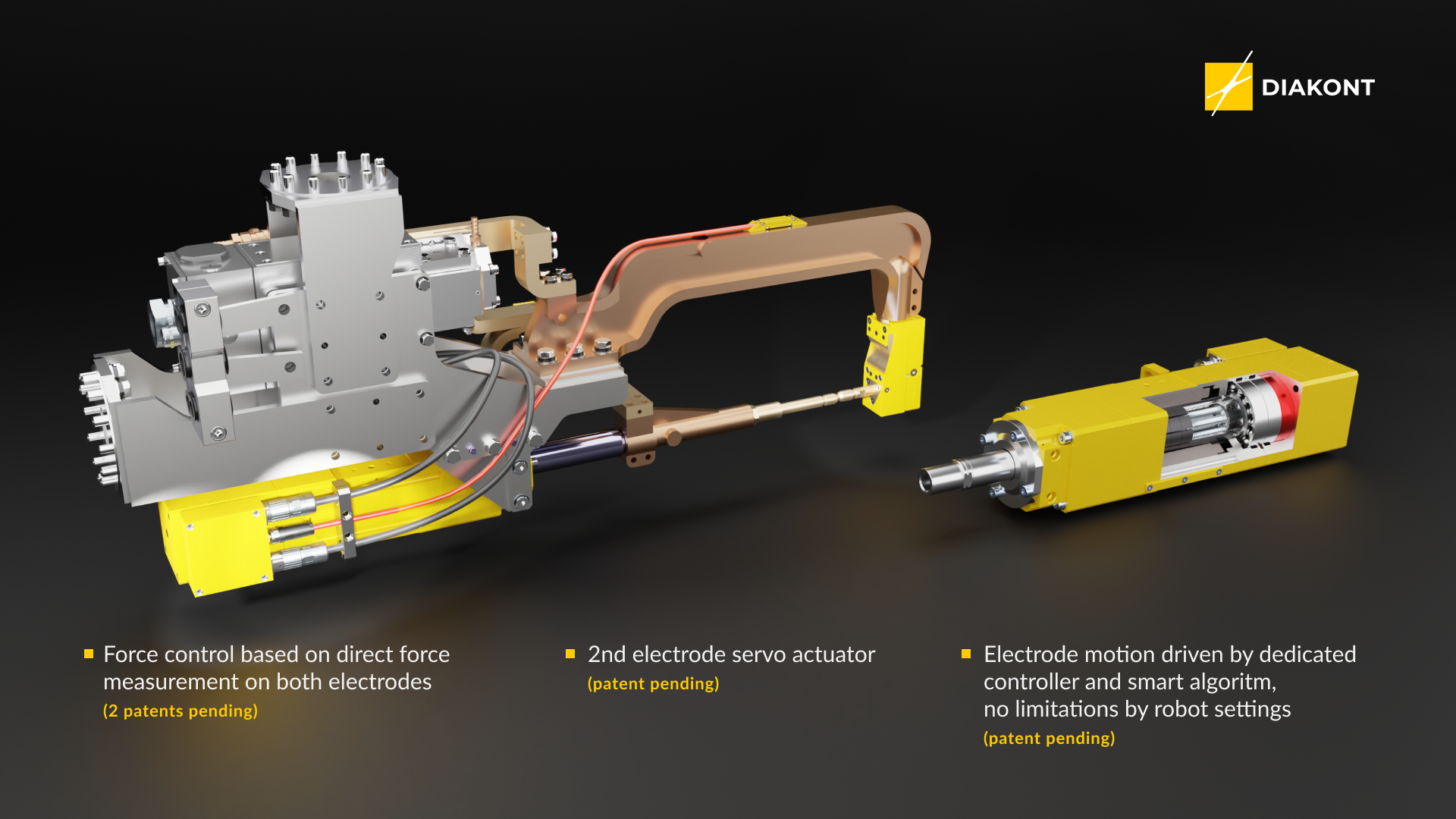
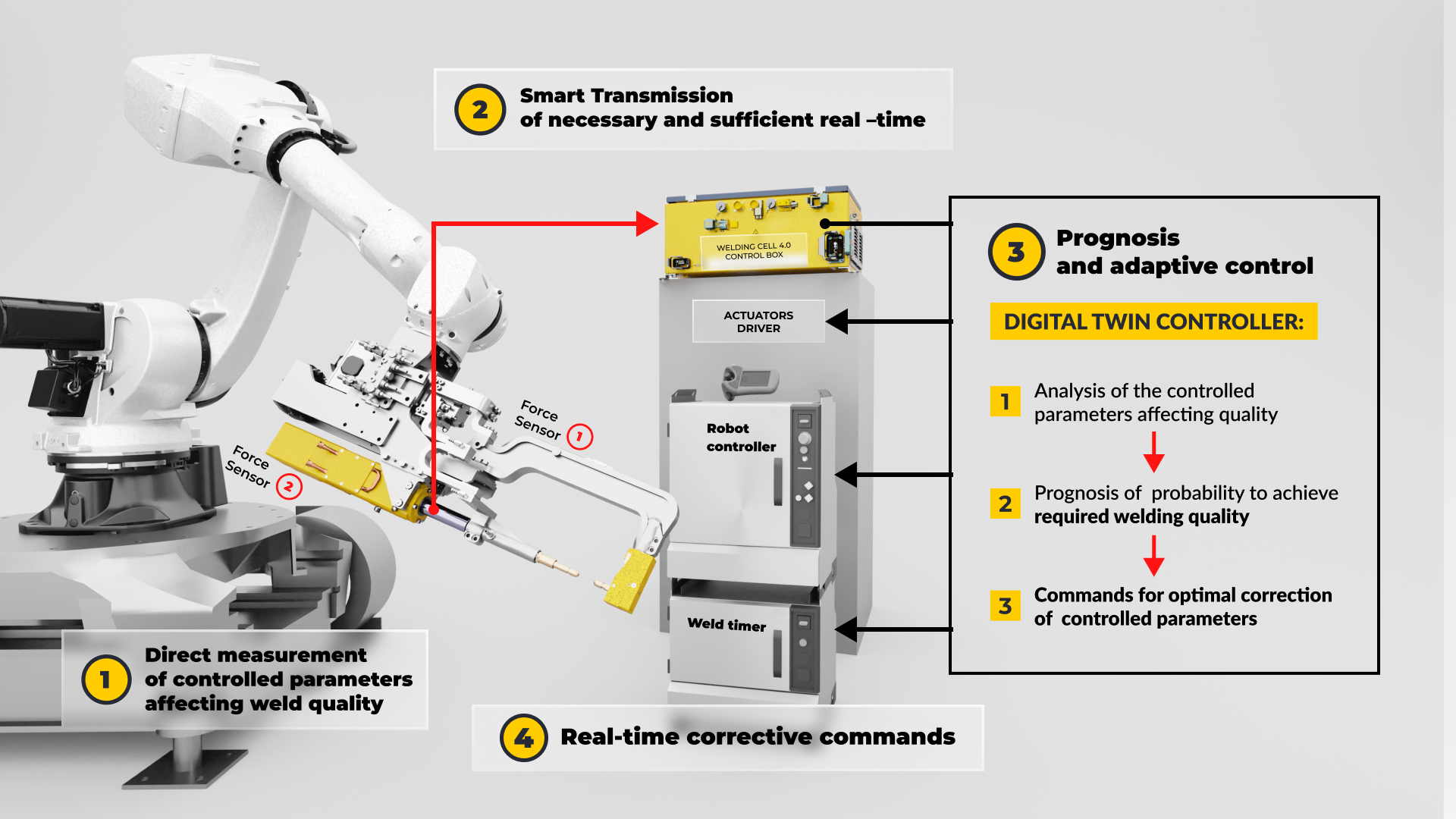
Thanks to the improved structure and control algorithms, the welding force with Welding Cell 4.0 system is maintained more accurately during the operation of the welding line.
To assess the stability of the force, comparative tests of a traditional cell with a KUKA robot (ServoGun Basic) and a Welding cell 4.0 were carried out. As a result of the test Welding Cell 4.0 showed a better force stability. The processes occurring during the operation of the cell - heating of the equipment or electrodes tips dressing – did not cause force deviation.
Moreover, difference of force on electrodes is also substantially lower thanks to the use of a second actuator with a separate force sensor.
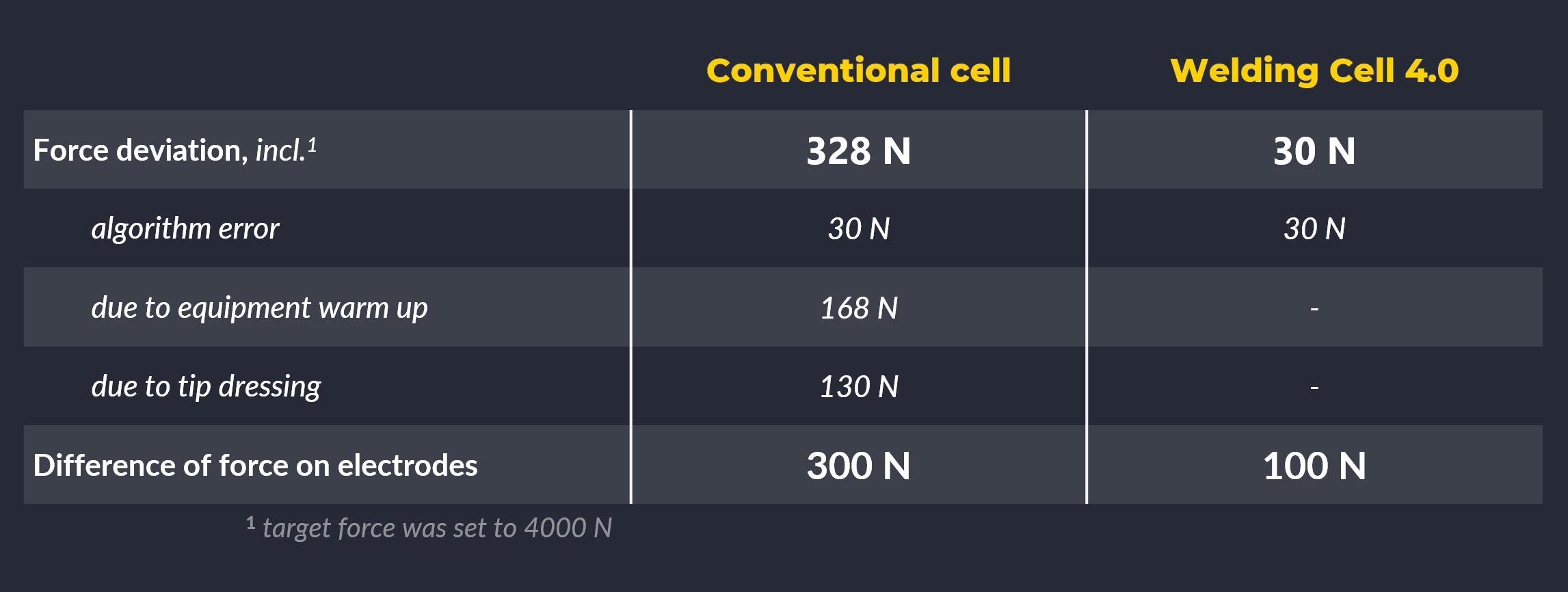
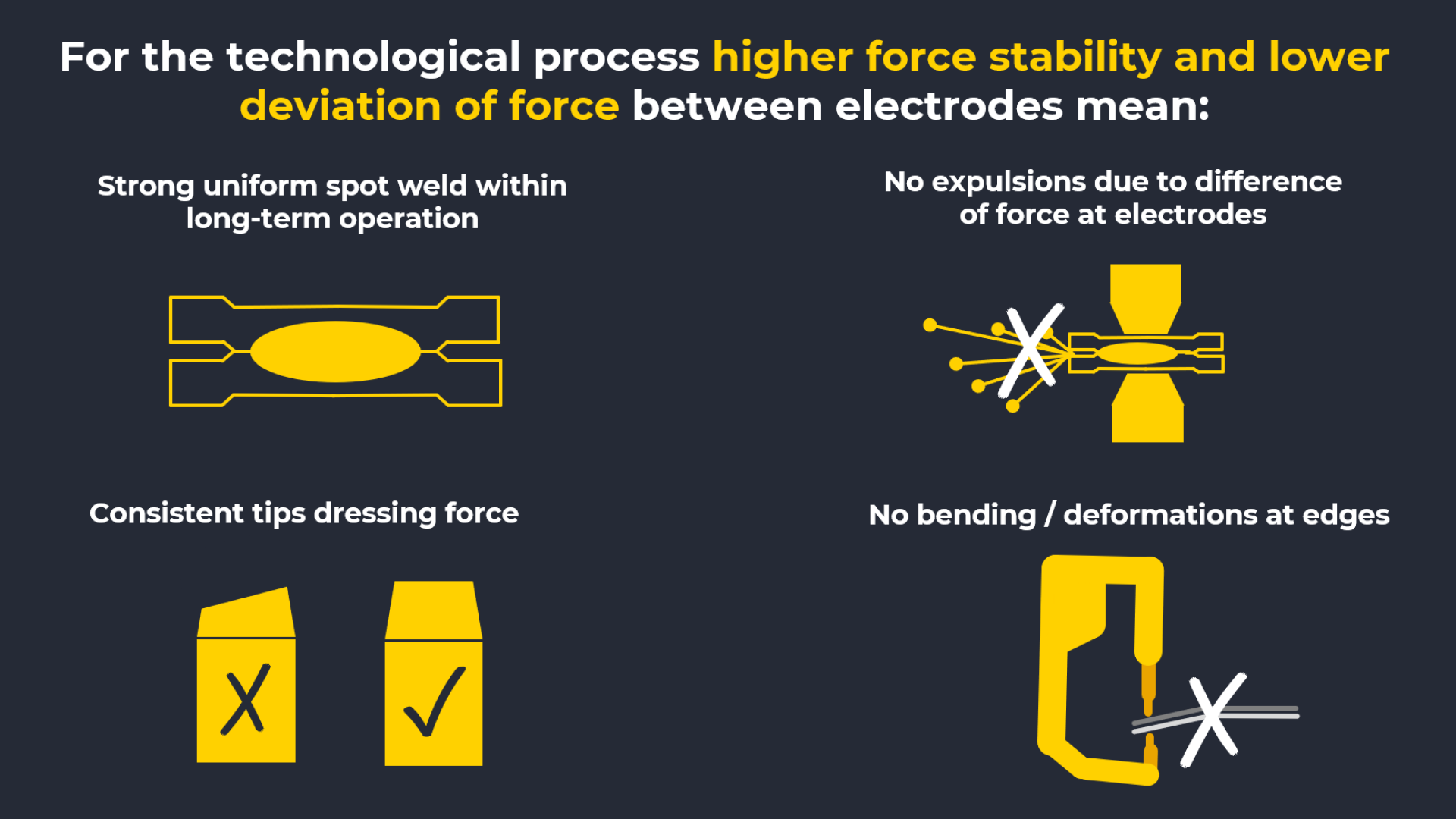
Tests of the Welding Cell 4.0 showed a reduction in the time for spot welding due to faster build-up and of force equalization, as well as closing and opening of the weld gun. Let’s compare a typical welding cycle performed by a conventional welding cell and Welding Cell 4.0 divided by stages of the cycle and see the results in time saving and increased productivity
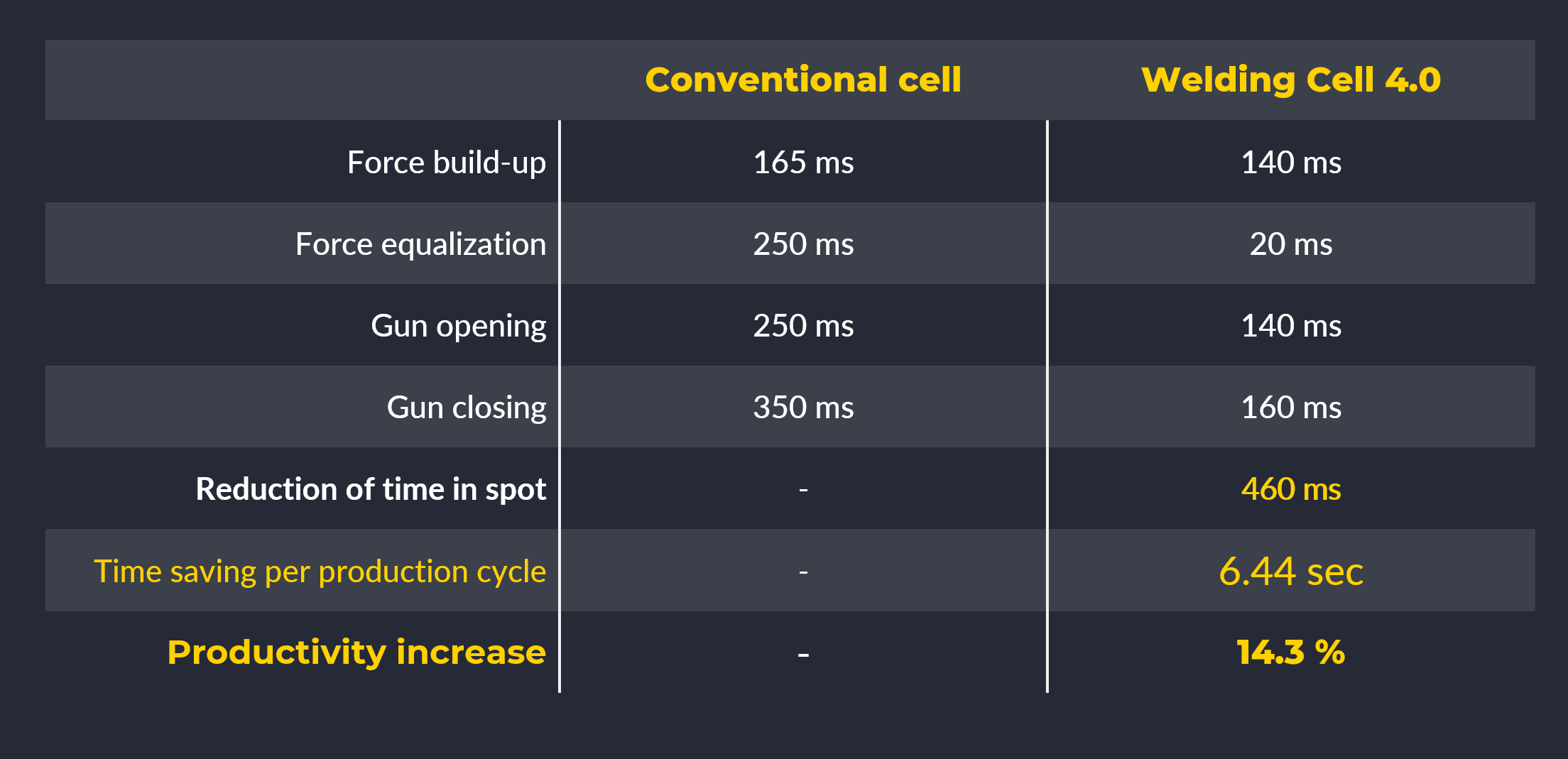
Besides the advantages within the welding cycle itself, thanks to two actuators at both electrodes of the welding gun, which are used in Welding Cell 4.0 and smart control algorithms it is possible to achieve productivity advantages also when considering overall welding program. For example, thanks to the optimized gun equalization technology with two moveable electrodes,
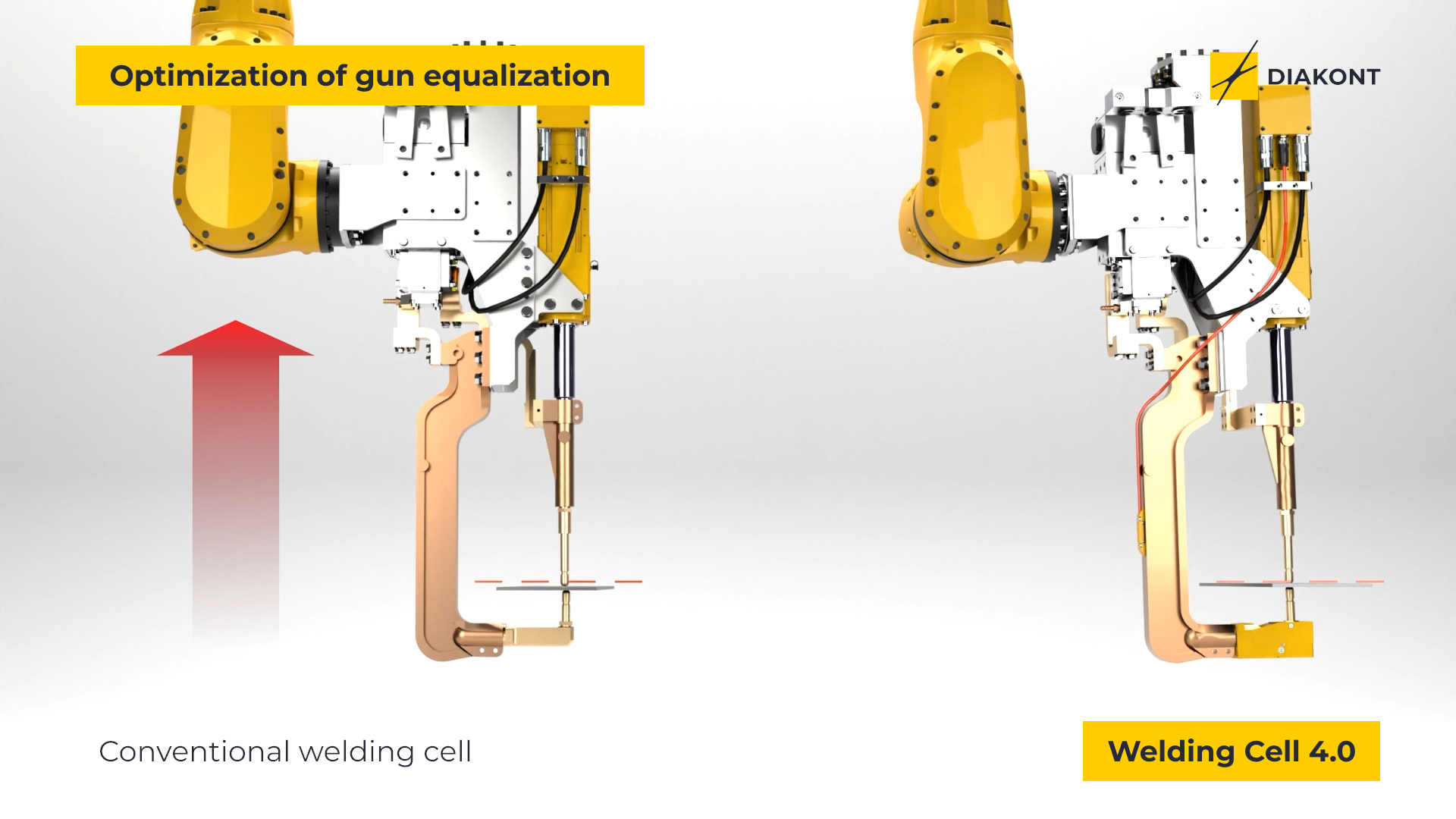
Additionally, it becomes possible for the robot to move the gun parallel to the surface of the welded parts and not lose time for precise and longer movements when approaching each welding spot. These smaller movements can be effectively performed by the actuators at each electrode. As a result,
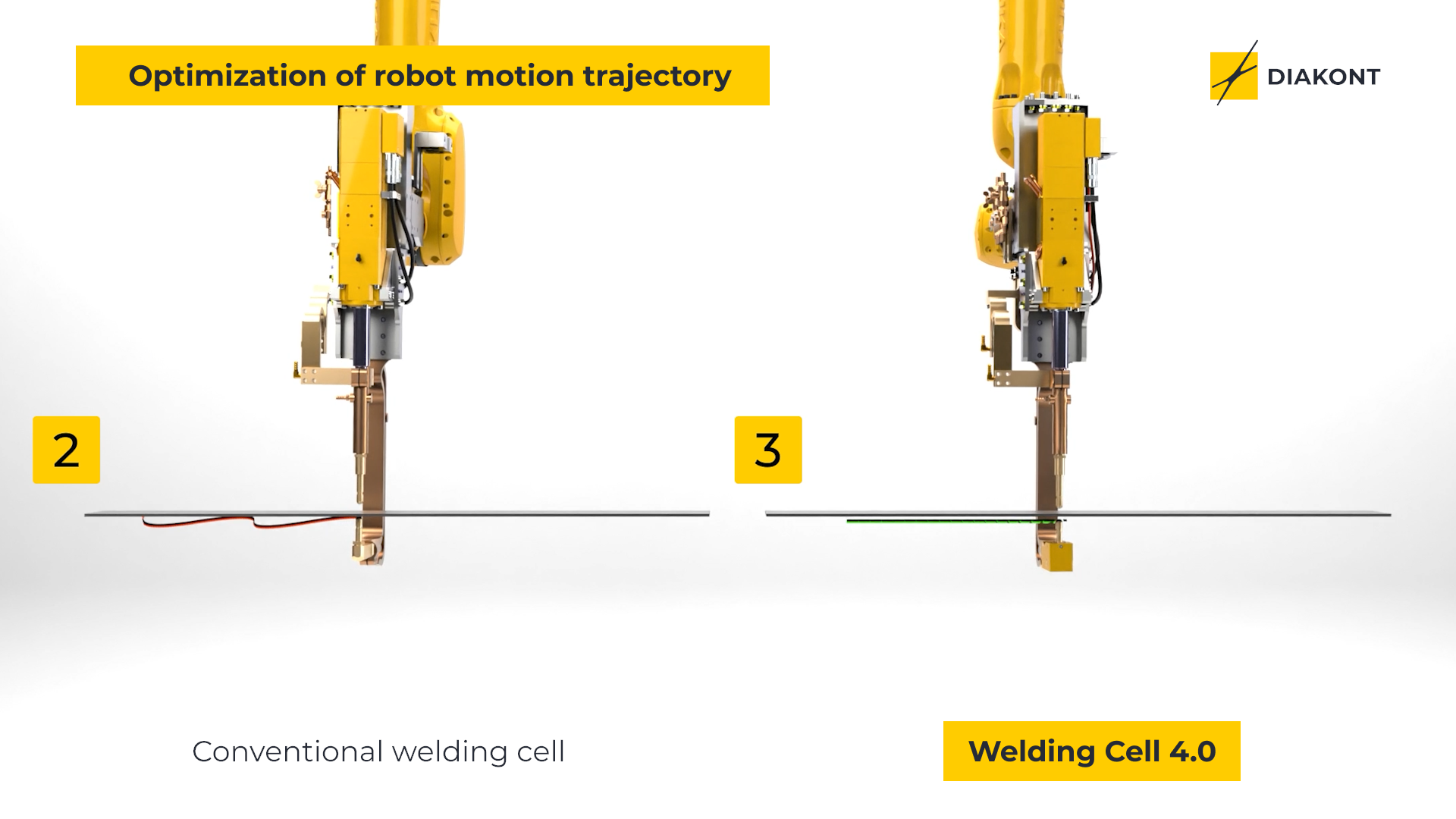
In order to evaluate the economic effect of "Welding Cell 4.0" implementation, an economical model of the robotic spot-welding line has been developed, which takes into account:
- Productivity changes
- Reduction in energy consumption
- Reduction of expenses related to reworking and control activities
- Reduction in the amount of maintenance required
- Reduction of the robotic spot-welding line cost
The estimate based on this model demonstrates substantial cost savings that "Welding Cell 4.0" provides:
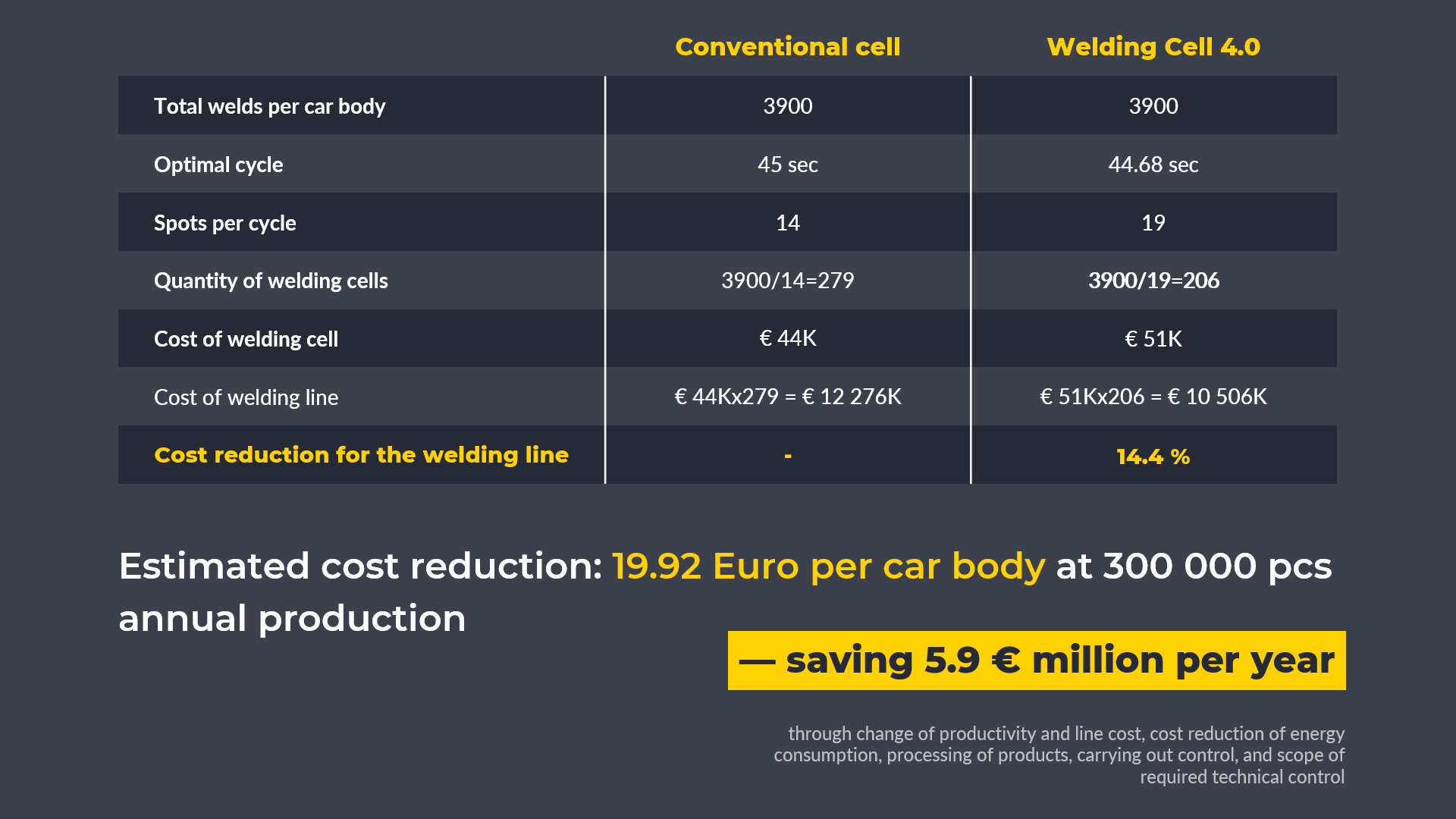