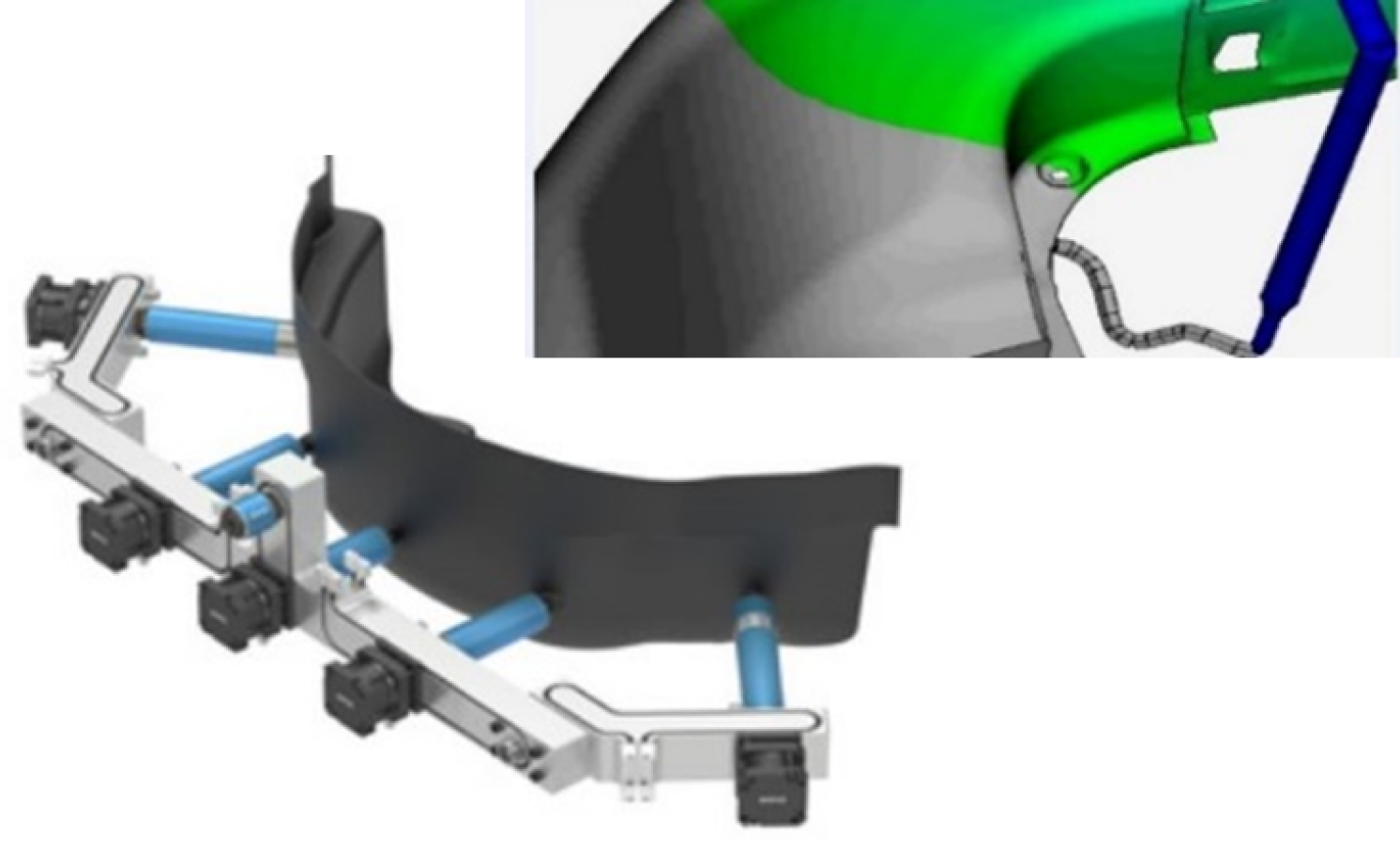
In sequential gating after the next gate is open, the flow front hesitates. Controlling the gate pin’s speed and position allows to keep pressure constant and the flow does not hesitate.
Servomotors provide quick pin repositioning between drops of different layers and simultaneous control over all pins through the control system allows to achieve much better quality of the parts. Precise control over each valve is provided by the servo-electric control system.

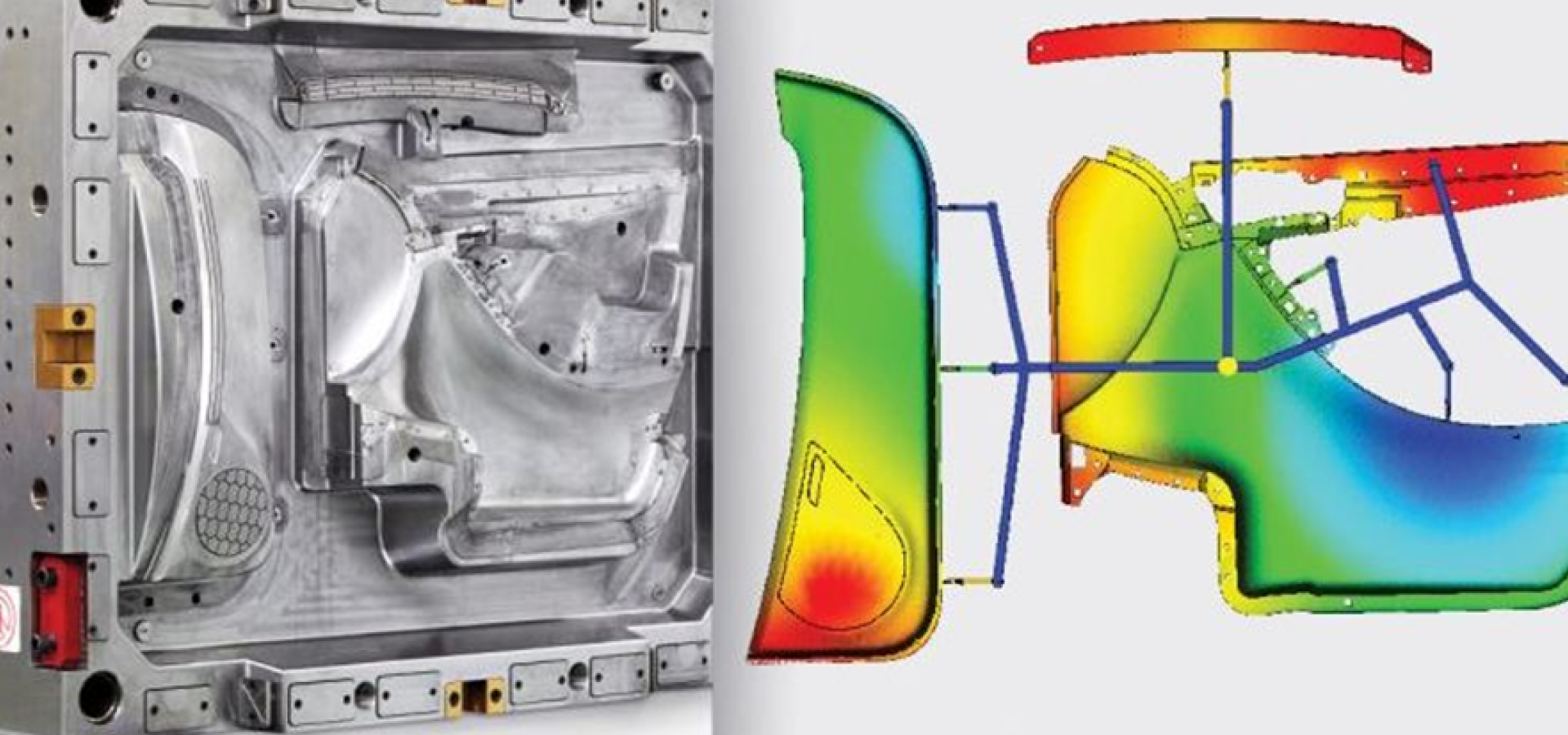
Pressure needed for the biggest parts is excessive for smaller ones; reducing the pressure correspondingly by partially opening the gate allows for part weight reduction. it can provide advantages for car body design, e.g. for EV vehicles.
High speed valve pin cycling quickly pushes away all material of previous color

- Servo valve gates are not prone to aging of cylinder seals, causing hydraulic system process variability
- Servo electric control eliminates process noise and drift without the need of complicated adjustments of the molding process by shop personnel.
Less clamping force is needed thanks to using cavity-by-cavity molding / splitting the pressure between the cavities depending on the cavity volume by setting individual gate openings.
Servo electric systems allow gate condition monitoring and prognosis to mitigate risk of unexpected production shutdown
Electric roller screw actuator, unlike pneumatic and hydraulic systems, does not require additional energy conversion to run the compressor and does not consume energy during pauses in operation, which reduces the cost of consumed electric energy by 3-4 times.
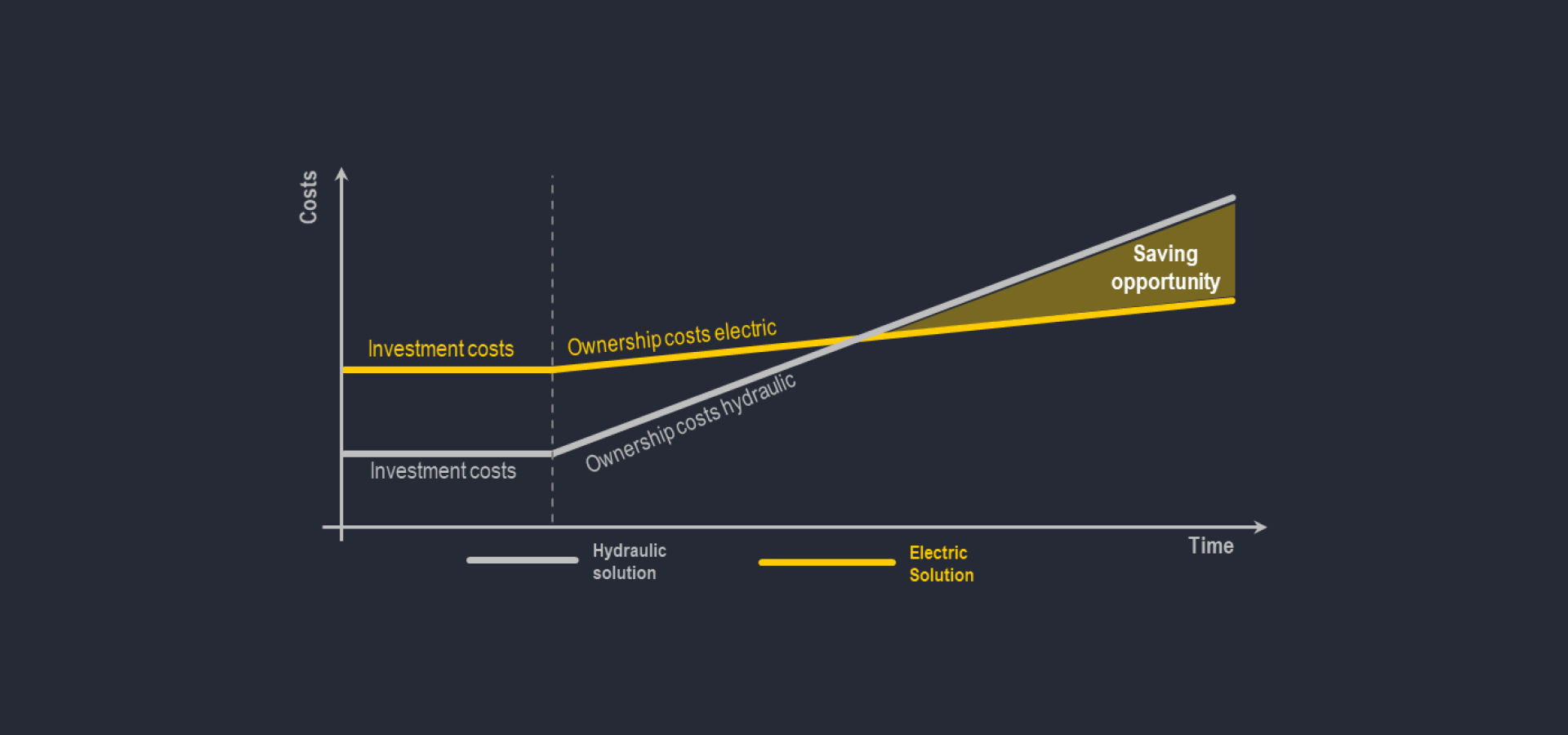

No risk of hydraulic oil mess inside the mold
No hydraulic oil production nor disposal is required